Hidden Challenge in Plastic Injection Moulding: Cushion Variation
- Shraddha Srivastava
- Nov 22, 2024
- 6 min read

Have you ever noticed inconsistencies in your plastic components? You’re not alone. Many companies that depend on high-quality plastic parts encounter this issue in injection moulding, often due to a factor known as "Cushion Variation." Cushion variation in plastic injection moulding is a common yet often overlooked issue that can lead to quality problems, including dimensional inaccuracies, surface defects, and unnecessary material waste.
In this blog, we’ll explore what cushion variation is, why it occurs, the problems it can cause, and, most importantly, how to manage it effectively. For any business that relies on precise plastic components, understanding and controlling cushion variation is crucial to ensure the quality of plastic products.
What is Cushion Variation in Plastic Injection Moulding?
In plastic injection moulding, the term "cushion" refers to the amount of molten plastic that remains in the barrel, in front of the screw, after the mould-filling and packing stages. The cushion is a critical part of the process, as it acts as a buffer between the screw and the barrel, ensuring consistent pressure application during the holding phase. However, when the cushion fluctuates from cycle to cycle, it leads to "cushion variation."
This inconsistency can have several negative effects on the moulding process. Cushion variation can cause problems such as uneven part quality, increased cycle times, reduced mould life, and material waste. To understand why cushion variation happens and how it can be controlled, let's explore some of the contributing factors.
The Problems Caused by Cushion Variation
1. Inconsistent Part Quality
One of the most noticeable consequences of cushion variation in plastic injection moulding is inconsistent part quality. When the cushion is not uniform, it can lead to parts with dimensional inaccuracies, surface defects, or insufficient part density. This inconsistency can be particularly problematic for companies that rely on high-precision plastic components for their products.
For example, in industries like automotive, electronics, or medical device manufacturing, precise plastic parts are crucial for ensuring the performance and safety of the final product. Cushion variation can result in parts that do not meet the necessary specifications, which leads to rework, scrap, or even product recalls.
2. Reduced mould Life
Excessive pressure fluctuations caused by cushion variation can put additional stress on the mould. Over time, this can accelerate mould wear and tear, leading to a reduced lifespan of the mould. When the cushion is inconsistent, the mould experiences higher than normal pressure during the injection and packing phases, which increases the likelihood of cracking or deformation.
For a plastic injection mould manufacturer in India, maintaining the mould's longevity is essential to reduce production costs. A worn-out mould means more frequent repairs or replacements, which can significantly increase operational expenses.
3. Increased Cycle Time
If the cushion is too small, the machine may require additional cycles to achieve the desired part quality. This results in increased production time, which affects overall efficiency. Companies striving for lean manufacturing and reduced cycle times will find that cushion variation disrupts their ability to meet production goals and deadlines.
4. Material Waste
Inconsistent cushion levels can lead to material waste. To compensate for fluctuating cushion variation, more material may be needed to ensure the part achieves the desired dimensions and quality. This results in unnecessary material consumption, increasing production costs and harming sustainability efforts.
Factors Contributing to Cushion Variation
Several factors can contribute to cushion variation, leading to issues in the injection moulding process. Understanding these factors is the first step in minimizing cushion variation and ensuring consistent part quality.
1. Machine Wear and Tear
Over time, wear and tear on the injection moulding machine, particularly the screw, barrel, and check valve, can affect the precision of material metering and pressure control. A worn-out screw may not deliver the correct amount of plastic, while a damaged check valve may not properly regulate the flow of material, leading to cushion fluctuations. Regular maintenance of these critical components can help reduce machine-related cushion variation.
2. Material Viscosity Variations
Material viscosity is another factor that can cause cushion variation. The viscosity of the plastic material can change due to fluctuations in temperature or material degradation. When the material’s viscosity changes, the amount of material required for the cushion can vary, leading to inconsistency in the moulding process. Maintaining consistent material temperature and moisture content is crucial to minimize viscosity-related cushion variation.
3. Mould design and Temperature
Mould design and temperature variations play a key role in cushion formation. If the mould design does not allow for proper venting or cooling, it can lead to pressure fluctuations during the packing and holding phases. Additionally, uneven cooling in the mould can result in inconsistent shrinkage, affecting the cushion and part quality.
4. Process Parameters
The injection speed, pressure, and holding time must be properly adjusted to ensure consistent cushion formation. If these parameters are not optimized, they can lead to variations in the cushion, causing issues in part quality. Regular monitoring and fine-tuning of these parameters are necessary to maintain consistent cushioning.
How to Minimize Cushion Variation
Minimizing cushion variation is critical to ensuring consistent part quality, reducing waste, and improving overall production efficiency. Here are some strategies for managing cushion variation in plastic injection moulding:
1. Regular Machine Maintenance
Regular maintenance is one of the most effective ways to reduce machine-related cushion variation. Ensuring that the screw, barrel, and check valve are in good condition is essential for maintaining consistent material flow and pressure control. Machine cleaning and lubrication should also be part of routine maintenance to improve the precision of the injection moulding process.
2. Consistent Material Handling
To maintain consistent viscosity and reduce cushion variation, material temperature and moisture content must be closely controlled. Using dryers and heaters to regulate material moisture and temperature can help maintain uniform viscosity, reducing fluctuations in the cushion.
3. Optimized Process Parameters
The injection speed, pressure, and holding time should be optimized to achieve consistent cushion formation. By carefully adjusting these process parameters, manufacturers can minimize cushion variation and improve part consistency. Automated systems that adjust these parameters in real time based on feedback can further help reduce cushion-related issues.
4. Mould Design Considerations
Mould design is another critical factor in reducing cushion variation. Designing moulds with proper venting and cooling systems helps to minimize pressure fluctuations and ensures that the cushion is consistent throughout the cycle. A well-designed mould also reduces the likelihood of inconsistent part shrinkage, further improving part quality.
5. Monitoring and Control
Advanced monitoring and control systems can provide real-time feedback on key process parameters like pressure, temperature, and material flow. By integrating sensors into the moulding system, manufacturers can track cushion formation and make adjustments in real time to maintain consistent quality.
Advanced Process Monitoring Techniques for Cushion Variation Control
Incorporating advanced monitoring techniques can significantly improve the ability to control cushion variation. Some key techniques include:
1. Cavity Pressure Sensing
Cavity pressure sensors provide real-time feedback on the pressure inside the mould cavity during the injection and packing phases. These sensors help detect variations in the cushion and allow operators to adjust process parameters accordingly.
2. Machine Learning and AI
Machine learning and AI can be used to predict potential issues based on historical data and real-time sensor readings. Predictive modelling and anomaly detection allow manufacturers to make proactive adjustments to prevent cushion variation before it becomes a problem.
3. Vibration Analysis and Infrared Thermography
Vibration analysis and infrared thermography can help detect mechanical issues and temperature variations that affect cushion formation. These techniques can identify potential problems early, enabling operators to take corrective actions before part quality is compromised.
Plastic Parts Manufacturing with Cushion Variation Control
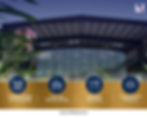
For companies that require plastic parts, working with a trusted plastic injection mould manufacturer in India, such as Vidhata Plastics, can ensure that cushion variation is effectively managed. Vidhata Plastics is a leading plastic parts manufacturer in India known for using advanced techniques to control cushion variation and produce high-precision plastic components. By partnering with Vidhata Plastics, you can rely on their expertise to deliver high-quality, consistent plastic parts, improving your production process and reducing costs.
Conclusion: Cushion variation in plastic injection moulding may seem like a small issue, but it can have a significant impact on part quality, production efficiency, and material waste. By understanding the factors that contribute to cushion variation and implementing effective strategies to minimize it, manufacturers can improve their injection moulding process and produce high-quality plastic parts consistently.
If you’re looking for a reliable plastic injection mould manufacturer in India, contact Vidhata Plastics today to learn more about how we can help streamline your plastic parts manufacturing process and minimize cushion variation for superior results.
Visit Our Website:Â https://www.vidhata.co.in/
Contact Us: https://www.vidhata.co.in/contact
Email Id: info@vidhata.co.in
WhatsApp No. : +919550665666