How High-Speed Machining in Plastic Injection Moulding Cuts Lead Times by 50%
- Shraddha Srivastava
- Dec 11, 2024
- 8 min read

Studies reveal that high-speed machining (HSM) can reduce mould production time by up to 50%, enabling companies to bring products to market faster without compromising quality. For businesses requiring moulds and plastic parts, HSM has become a vital tool for achieving precision, flexibility, and cost-effectiveness.
High-speed machining is an advanced manufacturing technique that employs high spindle speeds and rapid feed rates to efficiently remove material. Modern high-speed machining centres can achieve spindle speeds of up to 100,000 RPM or more. This technology plays a crucial role in the plastic injection moulding industry, facilitating the production of both plastic parts and injection moulds with remarkable efficiency.
In this blog, we will explore the concept of high-speed machining in plastic injection moulding, examine the latest advancements in the field, and discuss its numerous benefits.
What Is High-Speed Machining in Plastic Injection Moulding?
High-speed machining in plastic injection moulding is a manufacturing process that utilizes advanced machine tools, high-speed spindles, and specialized cutting tools to rapidly create injection moulds for plastic parts. This process is specifically designed to reduce production time while maintaining precision and quality.
The process involves the use of CAD/CAM software to design the moulds, high-speed CNC machines for material removal, and optimized cooling systems to enhance efficiency. This is particularly beneficial for companies that require complex mould designs with tight tolerances and smooth finishes, such as those in the automotive, electronics, and medical industries.
Advancements in High-Speed Machining in Plastic Injection Moulding
High-speed machining (HSM) has revolutionized the manufacturing of injection mould and plastic components, offering unparalleled speed, precision, and efficiency. Recent technological advancements have pushed the boundaries of what this process can achieve, enabling manufacturers to meet increasingly complex demands while reducing lead times and maintaining exceptional quality. Below, we explore the latest technical innovations in high-speed machining that are transforming the manufacturing landscape.
Advanced Machine Tools
Direct-Drive Spindles Direct-drive spindles eliminate the limitations of traditional belt-driven systems by providing superior responsiveness and accuracy. They enable higher rotational speeds, smoother operations, and enhanced machining precision, making them ideal for intricate mould details.
Thermal Compensation Systems Thermal compensation systems actively monitor and adjust for temperature fluctuations in machine tools. This reduces the impact of thermal expansion or contraction, ensuring consistent dimensional accuracy and superior part quality.
Multi-Tasking Machines These advanced machines integrate multiple operations such as milling, drilling, and turning into a single platform. By minimizing setup times and tool changes, they significantly enhance productivity and streamline the manufacturing process.
Innovative Cutting Tool Technology
Advanced Coatings for Cutting Tools Cutting tools with advanced coatings like Physical Vapor Deposition (PVD) and Chemical Vapor Deposition (CVD) provide enhanced wear resistance, heat dissipation, and durability. These properties are crucial for maintaining efficiency and precision during high-speed machining.
Optimized Tool Geometries Cutting tool manufacturers have refined tool geometries to improve cutting performance. Features such as sharper cutting edges and specialized flute designs reduce cutting forces, improve chip evacuation, and enhance surface finishes.
Intelligent Tool Monitoring Systems Real-time tool monitoring systems use sensors to track tool wear and performance. These systems enable predictive maintenance, reducing unplanned downtime and extending tool life for consistent machining quality.
3D Printing and Additive Manufacturing Integration
Hybrid Manufacturing By combining HSM with additive manufacturing, manufacturers can produce intricate mould components with reduced material waste and faster lead times. For example, 3D printing can create complex inserts that are later finished with high-speed machining, blending the strengths of both technologies.
Prototype Development 3D printing allows rapid production of prototypes for mould components. This capability accelerates design iterations, reduces costs, and ensures that final machining processes are optimized for precision.
Optimized Cooling Systems
Modern cooling systems embedded within injection moulds enhance heat dissipation during machining and moulding processes. Advanced cooling channels facilitate rapid heat removal, reducing cycle times and boosting production rates without compromising mould quality.
High-Precision CNC Controls
High-Performance CNC Systems: The latest CNC systems provide unmatched precision, enabling manufacturers to execute complex machining operations with minimal tolerances. These systems ensure superior surface finishes, even for the most intricate mould details.
AI-Powered CAM Software: Artificial intelligence (AI) in CAM software automates tool path optimization, reducing programming time and improving overall machining efficiency. It enhances decision-making by adapting to material properties and design complexities.
Digital Twin Technology
Digital twins create virtual replicas of machines and processes, enabling manufacturers to simulate and optimize machining operations before production begins. This minimizes errors, reduces waste, and ensures optimal performance during high-speed machining.
Multi-Axis Machining
High-speed machining has embraced multi-axis technology, with machines featuring five or more axes for greater flexibility. These machines can machine complex 3D geometries directly on moulds, eliminating the need for secondary processes and enhancing design capabilities.
Industry 4.0 Integration
IoT and Big Data: IoT-enabled sensors collect real-time data on machine performance, cutting parameters, and environmental factors. Big data analytics then use this information to optimize machining conditions, predict maintenance needs, and improve overall efficiency.
Automation and Robotics: Automation systems, including robotic arms for material handling, improve production consistency and reduce labor costs. These technologies are seamlessly integrated into high-speed machining operations, enabling round-the-clock productivity.
Advanced Materials for Mould Components
Manufacturers are increasingly using high-performance materials, such as tool steels with enhanced thermal conductivity and wear resistance, for injection moulds. Additionally, fiber-reinforced composites are being incorporated for lightweight yet durable mould components, further enhancing machining efficiency.
Real-Time Monitoring and Feedback Systems
Sensors embedded in machining systems monitor critical parameters such as spindle speed, temperature, and vibration. This real-time feedback allows manufacturers to make proactive adjustments, ensuring high-quality results and minimizing material waste.
High-speed machining has evolved into a highly sophisticated process, driven by a combination of advanced machine tools, innovative software, cutting-edge materials, and Industry 4.0 technologies. These advancements empower manufacturers to accelerate production while achieving greater precision, reduced costs, and improved quality.
Key Tools and Technologies in High-Speed Machining
High-speed machining (HSM) for plastic injection moulds is a sophisticated process that combines advanced machinery, cutting-edge tools, and intelligent software. These components work together to deliver unparalleled efficiency, precision, and productivity. Below, we delve into the essential tools and technologies driving this innovation.
High-Performance CNC Machine Tools
High-Speed Spindles: High-speed spindles are the cornerstone of modern CNC machines, enabling rapid rotation rates that support efficient material removal. Their precision is critical for maintaining surface quality during fast machining.
Rigid Machine Structures: A robust machine frame is fundamental to minimizing vibrations during operations. Reduced vibrations ensure dimensional accuracy and consistency, even during high-speed cuts.
Advanced CNC Controls: Modern CNC systems integrate advanced algorithms to optimize tool paths, feed rates, and spindle speeds. This not only shortens machining cycles but also enhances precision in the production of intricate mould components.
High-Performance Cutting Tools
Indexable Inserts: These replaceable inserts offer flexibility and cost-effectiveness. They allow for quick tool changes, reducing downtime and maintaining continuous production.
Solid Carbide End Mills: Known for their rigidity and sharpness, solid carbide end mills are ideal for producing intricate details with high precision.
Ball-Nose End Mills: These tools are specifically designed for machining curved surfaces and rounded corners, ensuring smooth finishes in complex mould geometries.
Drill Bits: Drill bits in high-speed machining are engineered for various sizes and depths, ensuring precise and efficient hole creation for mould components.
Advanced Cutting Tool Materials and Coatings
Carbide Materials: Carbide tools offer exceptional hardness and wear resistance, making them a popular choice for high-speed machining.
Ceramic Tools: Ceramic cutting tools excel in high-temperature stability and wear resistance, allowing for efficient machining under demanding conditions.
PCD (Polycrystalline Diamond): PCD tools provide unmatched cutting performance, edge retention, and durability, especially for abrasive materials.
Diamond-Like Carbon (DLC) Coatings: DLC coatings reduce friction between the tool and the material, improving tool life and achieving smoother finishes.
Cooling and Lubrication Systems
High-Pressure Coolant Systems: High-pressure coolant systems remove heat and chips effectively from the cutting zone. This helps maintain tool integrity and ensures a consistent machining process.
MQL (Minimum Quantity Lubrication): MQL systems significantly reduce coolant consumption by applying only the required amount of lubricant. This improves the environmental impact of high-speed machining while maintaining efficiency.
Advanced CAM Software
Optimized Tool Path Generation: CAM software creates highly efficient tool paths, reducing cutting time and maximizing material removal rates. It also minimizes manual intervention, ensuring a seamless workflow from design to production.
Intelligent Simulation Features: Modern CAM software includes simulation tools that allow manufacturers to visualize the machining process virtually. This minimizes errors and ensures that actual production matches design specifications.
Benefits of High-Speed Machining in Plastic Injection Moulding
For companies that require plastic parts, adopting high-speed machining in plastic injection moulding offers several key advantages:
1. Reduced Lead Times
High-speed machining drastically cuts down the time required to create injection moulds. Faster mould production enables manufacturers to bring new products to market more quickly, giving companies a competitive edge.
2. Improved Precision
HSM allows for the creation of intricate mould designs with tight tolerances, ensuring that the final plastic parts meet exact specifications. This precision is especially important for industries like medical devices and electronics.
3. Enhanced Productivity
By combining faster machining cycles with intelligent tools and software, HSM significantly increases overall productivity. This allows manufacturers to handle larger volumes without compromising on quality.
4. Cost Savings
While the initial investment in HSM technology can be high, the long-term savings are significant. Faster production cycles, reduced tool wear, and fewer errors translate to lower operational costs.
5. Design Flexibility
HSM makes it easier to produce complex and unique mould designs that were previously challenging or impossible to create with traditional machining methods.
High-Speed Machining Process: A Step-by-Step Overview
The high-speed machining process for injection moulds follows a structured approach to ensure quality and efficiency:
1. Design Phase
CAD software is used to design the mould, considering the geometry of the plastic part and material properties.
CAM software generates the tool paths for high-speed machining.
2. Machine Setup
The mould material is securely clamped to the machine table.
Cutting tools and coolant systems are prepared for operation.
3. Machining Operations
Roughing: Large cutting tools remove the bulk of the material at high speeds.
Finishing: Smaller tools create the intricate details and smooth surfaces required for the mould.
4. Inspection and Quality Control
Dimensional and surface finish inspections are performed to ensure the mould meets specifications.
Plastic Injection Mould Manufacturer in India with Latest technology in High Speed Machining
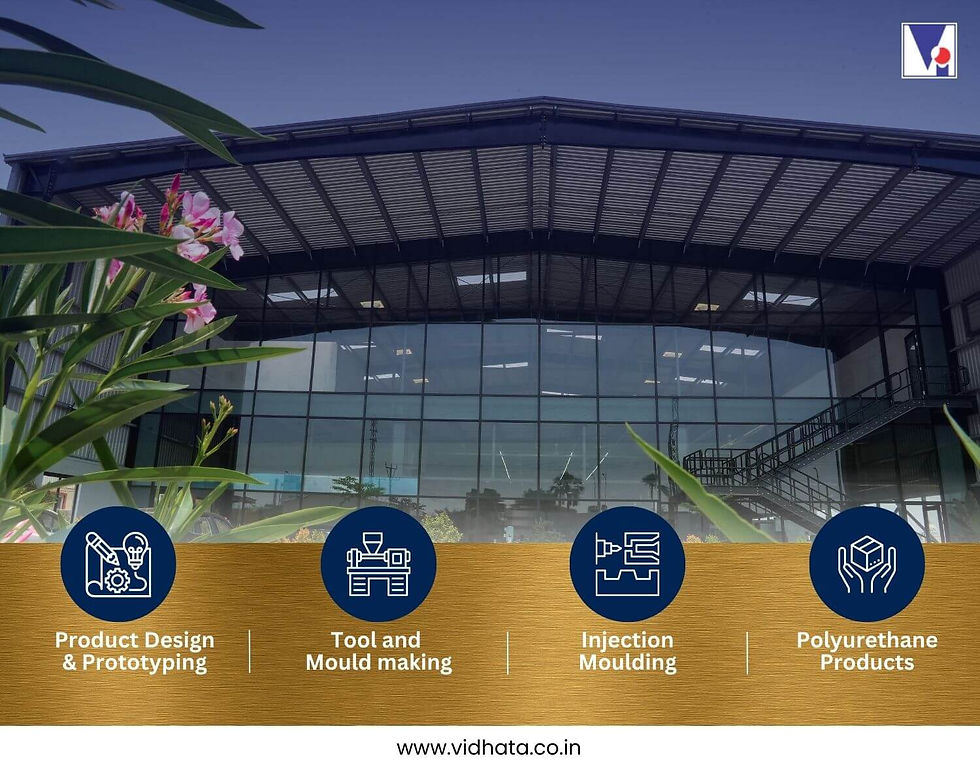
When it comes to high-speed machining in plastic injection moulding, Vidhata Plastics stands out as a trusted name. As a leading plastic injection mould manufacturer in India and plastic parts manufacturer in India, Vidhata Plastics employs state-of-the-art high-speed machining techniques to deliver high-quality moulds and parts.
Their commitment to innovation, precision, and customer satisfaction makes them the preferred choice for companies that require moulds for manufacturing plastic parts. Vidhata Plastics leverages advancements in high-speed machining to reduce lead times, improve product quality, and offer greater design flexibility.
Whether you need injection moulds for plastic parts or custom-designed plastic components, Vidhata Plastics ensures that every product meets the highest standards of excellence.
Conclusion: High-speed machining in plastic injection moulding is transforming the way injection moulds for plastic parts are designed and manufactured. From faster lead times and enhanced precision to cost savings and improved productivity, the benefits are undeniable.
For companies that require moulds and plastic parts, partnering with a trusted plastic injection mould manufacturer in India like Vidhata Plastics ensures that you harness the full potential of this revolutionary technology.
Ready to experience the future of plastic manufacturing? Contact Vidhata Plastics today and let us help you bring your ideas to life with precision and speed.
Visit Our Website: https://www.vidhata.co.in/
Contact Us: https://www.vidhata.co.in/contact
Email Id: info@vidhata.co.in
WhatsApp No. : +919550665666
Comments