Injection Moulding Defects: Causes, Fixes, and Prevention Strategies
- Shraddha Srivastava
- Mar 25
- 5 min read
Introduction
Plastic injection moulding is the backbone of high-precision plastic parts manufacturing, enabling mass production of complex components in automotive, medical, aerospace, electronics, and industrial applications. However, the process is susceptible to various injection moulding defects, leading to compromised structural integrity, functional failures, and increased production costs.
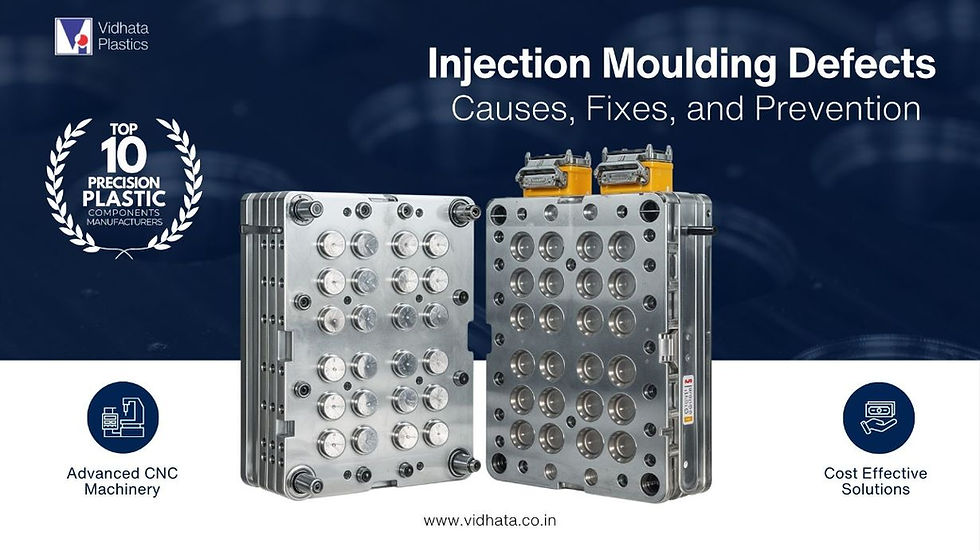
Studies indicate that nearly 30% of injection-moulded parts are rejected due to defects caused by poor process control, material inconsistencies, and mould design flaws. For industries relying on precision plastic parts manufacturing, preventing these defects is critical to achieving consistent quality, reduced waste, and enhanced production efficiency.
This comprehensive guide explores common injection moulding defects, their root causes, preventive measures, and advanced solutions for defect-free plastic parts manufacturing.
Common Injection Moulding Defects
1.1 Short Shots
Technical Description:
A short shot occurs when the molten polymer fails to fill the mould cavity, resulting in incomplete or structurally deficient components. This defect is critical in high-tolerance plastic parts manufacturing, where dimensional accuracy and mechanical load distribution are essential. Short shots significantly impact material cohesion, part durability, and downstream assembly compatibility.
Root Causes:
Inadequate injection pressure: Insufficient force reduces polymer penetration into intricate or thin-walled sections, leading to incomplete fill.
Rapid polymer solidification: High-crystallinity polymers or suboptimal melt temperatures cause premature material solidification before full cavity occupation.
Entrapped gases and backpressure: Poor mould venting creates air pockets, obstructing material flow and resulting in unfilled voids.
Viscosity inconsistencies: Variations in molecular weight distribution, temperature gradients, or additive dispersion impact rheological behavior, reducing polymer flow efficiency.
Prevention Strategies:
✔ Increase injection pressure and hold time to compensate for viscosity-induced flow resistance.
✔ Integrate vacuum-assisted venting to eliminate trapped air and pressure fluctuations.
✔ Use tailored polymer blends with controlled viscosity profiles to enhance flow characteristics.
✔ Employ multi-point gating systems to distribute material across complex geometries evenly.
Advanced Solution:
Real-time cavity pressure monitoring with adaptive flow control dynamically adjusts injection velocity and hold pressure, ensuring optimal material fill and eliminating short shots.
1.2 Warpage and Distortion
Technical Description:
Warpage arises due to non-uniform shrinkage stresses, causing part deformation that deviates from intended design specifications. This is particularly critical in structural or load-bearing plastic components, where dimensional deviations compromise assembly fit and stress distribution.
Root Causes:
Asymmetric shrinkage gradients: Variations in polymer cooling rates induce internal stress differentials, leading to non-uniform deformation.
Inefficient cooling system design: Suboptimal thermal dissipation mechanisms result in localized residual stresses, promoting warpage.
Anisotropic fiber orientation in reinforced plastics: Uncontrolled molecular alignment in polymer composites generates directional shrinkage inconsistencies.
Prevention Strategies:
✔ Implement conformal cooling channels with optimized thermal gradients for uniform shrinkage control.
✔ Optimize fibre reinforcement orientation through controlled melt flow kinematics.
✔ Calibrate packing pressure profiles to balance internal stress distribution.
Advanced Solution:
Advanced Mould Flow Analysis (MFA) and Finite Element Modeling (FEM) predict and correct shrinkage differentials preemptively, allowing precise compensation in mould cavity design and polymer selection.
1.3 Sink Marks and Voids
Technical Description:
Sink marks form when differential cooling rates cause surface depressions, while voids occur due to localized material shrinkage or trapped gases, both of which severely impact surface integrity and internal material density.
Root Causes:
Uncompensated volumetric shrinkage: Inadequate melt packing pressure causes polymer contraction before full material consolidation.
Thermal gradient inconsistencies: Non-uniform cooling cycles prevent material from solidifying evenly, leading to surface distortions.
Gas entrapment within thick-walled regions: Incomplete melt densification allows void formation due to pressure differentials.
Prevention Strategies:
✔ Adjust pressure profiling to maintain uniform compaction during polymer solidification.
✔ Incorporate foamed polymers or microcellular injection moulding techniques to balance shrinkage dynamics.
✔ Design balanced thermal pathways to prevent localized shrinkage variations.
Advanced Solution:
Real-time predictive shrinkage compensation systems continuously modulate melt packing parameters, ensuring homogeneous material consolidation.
1.4 Flash Formation
Technical Description:
Flash occurs when molten polymer escapes through unintended gaps in the mould interface, leading to excess material deposition along parting lines or ejection sites. This defect compromises precision tolerances and increases post-processing requirements.
Root Causes:
Excessive injection pressure relative to clamping force: High packing pressure differentials force material into unintended areas.
Wear-induced mould misalignment: Progressive degradation of sealing surfaces and guide pins allows material seepage.
Inadequate parting line engineering: Improperly designed sealing interfaces provide leakage pathways.
Prevention Strategies:
✔ Optimize injection-to-clamping force ratio to prevent over-packing.
✔ Maintain zero-clearance parting lines through ultra-precision CNC machining.
✔ Apply localized reinforcement coatings on high-wear mould surfaces.
Advanced Solution:
In-situ laser surface conditioning ensures sub-micron parting line tolerances, eliminating leakage risks.
1.5 Weld Lines
Technical Description:
Weld lines form where separate melt fronts converge but fail to fully bond, creating mechanically weak zones with poor polymer interdiffusion. These defects significantly compromise impact resistance and structural integrity.
Root Causes:
Low polymer temperature at flow junctions: Reduced molecular diffusion inhibits cohesive bonding.
Turbulent flow interface conditions: Disordered melt front interactions lead to incomplete material fusion.
Surface contamination: Foreign particulates disrupt molecular entanglement, preventing strong adhesion.
Prevention Strategies:
✔ Increase polymer melt temperature and shear heating at flow convergence zones.
✔ Re-engineer gate locations to direct material flow paths optimally.
✔ Employ high-purity resins with uniform molecular weight distribution.
Advanced Solution:
Localized inductive heating of weld line areas enhances interfacial adhesion by promoting polymer chain entanglement at the molecular scale.
1.6 Jetting
Technical Description:
Jetting results from high-velocity molten polymer injection, leading to turbulent flow disruptions and randomized stress accumulation in the part structure. This defect is highly detrimental in micro-featured plastic parts where surface uniformity is critical.
Root Causes:
Excessive initial injection velocity: Rapid material entry prevents smooth laminar flow, causing jetting artefacts.
Suboptimal gate positioning: Poor gate placement induces uncontrolled flow acceleration, increasing turbulence intensity.
Inappropriate melt viscosity selection: Inadequate rheological optimization exacerbates shear instabilities.
Prevention Strategies:
✔ Reduce initial injection velocity to maintain controlled melt propagation.
✔ Reposition gate locations to facilitate gradual cavity filling.
✔ Optimize shear-sensitive polymer formulations for reduced turbulence susceptibility.
Advanced Solution:
Sequential valve gating (SVG) technology dynamically regulates polymer entry points, maintaining controlled flow symmetry and eliminating jetting artefacts.
Industry Leader in Defect-Free Plastic Parts Manufacturing
As a leading plastic parts manufacturer in India, Vidhata Plastics employs advanced plastic injection moulding techniques to eliminate defects and ensure high-performance plastic components.
Our expertise includes:
✔ AI-driven process control, detecting and correcting defects in real-time.
✔ Advanced mould flow simulation, optimizing gate placement and cooling strategies.
✔ High-precision mould fabrication, ensuring zero-clearance sealing to prevent flash.
✔ Microcellular foaming technology, reducing shrinkage-induced defects.
Vidhata Plastics provides defect-free plastic parts for automotive, medical, electronics, and industrial applications, setting the benchmark for precision plastic parts manufacturing.
Conclusion
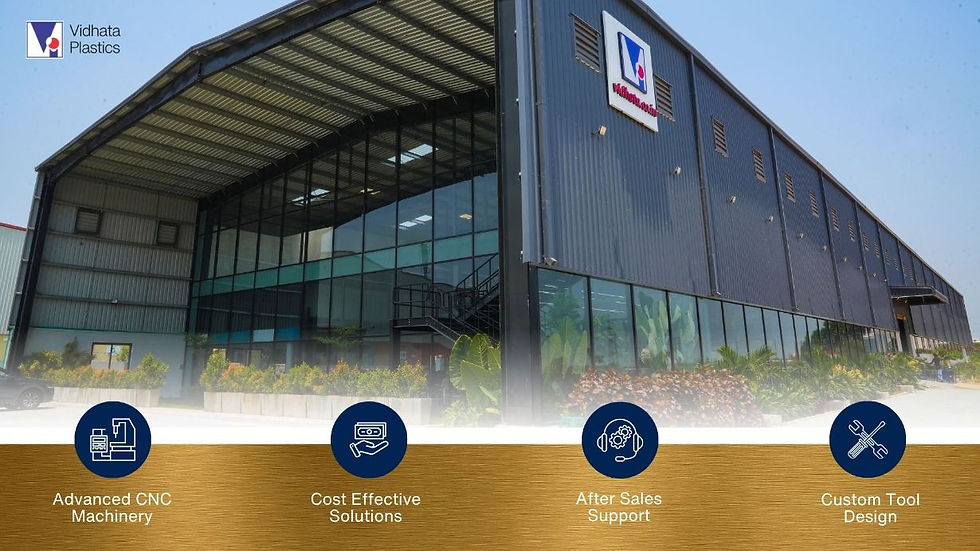
Preventing plastic injection moulding defects is crucial for ensuring high-precision, durable, and functionally reliable plastic parts. By integrating real-time process monitoring, AI-driven defect detection, and precision-engineered mould designs, manufacturers can achieve zero-defect production. Advanced techniques such as cavity pressure sensors, conformal cooling, and rheological flow analysis optimize material distribution and shrinkage control, eliminating defects like short shots, warpages, sink marks, and weld lines.
As a leading plastic parts manufacturer in India, Vidhata Plastics specializes in precision-driven plastic injection moulding solutions tailored for automotive, medical, and industrial applications. Our expertise in high-accuracy mould fabrication and smart polymer processing ensures defect-free production with superior dimensional stability and mechanical integrity.
📞 Contact Vidhata Plastics, the trusted plastic injection mould manufacturer in India, for high-precision, defect-free plastic parts manufacturing!
Visit Our Website: https://www.vidhata.co.in/
Contact Us: https://www.vidhata.co.in/contact
Email Id: info@vidhata.co.in
WhatsApp No. : +919550665666
Comments