The Power of Automating Laser Technology for Mould Repair
- Shraddha Srivastava
- Oct 23, 2024
- 6 min read

Did you know that 60% of delays in plastic manufacturing are caused by mould problems? In this fast-moving industry, keeping moulds in good shape is key to maintaining product quality and avoiding costly downtime. Traditional methods of repairing moulds can take a lot of time and may not offer the precision needed for today’s production demands.
However, automating laser technology for mould repair has changed the game. This advanced technology provides a faster, more accurate, and cost-effective way to fix moulds. It’s especially useful for industries like automotive, electronics, and consumer goods that depend on high-quality plastic parts.
In this blog, we’ll explain how laser welding technology, combined with automation, is making mould repairs easier, improving efficiency, and cutting costs.
What is Automating Laser Technology for Mould Repair?
Laser welding is a precise method that uses a high-energy laser beam to repair damaged moulds by melting and fusing material. Compared to traditional methods like TIG welding, laser welding offers greater accuracy and less heat distortion.
For industries relying on plastic parts, especially in injection moulding, this technology helps restore moulds without disrupting production. Automating the repair process with laser technology enhances efficiency, precision, and consistency. By using robotic systems, vision systems, and advanced software, manufacturers can streamline repairs, improving accuracy and reducing labor costs. This is especially useful for plastic injection mould manufacturers in India, ensuring quality in mould production.
Key Components of Automating Laser Technology for Mould Repair
Automating laser technology for mould repair uses advanced equipment and systems to make the repair process faster, more precise, and more efficient. Here are the main parts that make this system work:
1. Robotic Arm:
Precise Movement: The robotic arm can accurately move the laser to the exact spot that needs repair.
Flexibility: It can be programmed to move in complex ways and adjust to different mould shapes.
Strength: The arm is strong enough to carry the laser head and any extra tools.
2. Laser Welding Head:
Power: The laser needs enough power to melt and fuse the material of the mould for proper repair.
Beam Quality: The laser beam must be sharp and steady to ensure precise welding.
Wavelength: The laser's wavelength should match the type of material being repaired, like metal or plastic.
3. Vision System:
Capturing Images: The vision system takes pictures of the mould to find the damaged areas.
Analyzing Damage: Special software analyzes the images and tells the robotic arm where to move.
Real-time Updates: The vision system provides feedback during the repair, allowing the arm to adjust as needed.
4. Control System:
Programming: The control system programs the robotic arm's movements and manages the laser settings.
User Interface: The system is easy to use, letting operators input repair instructions and watch the process.
Integration: The control system connects all parts of the automated system, ensuring everything works smoothly.
5. Safety Features:
Emergency Stop: An emergency button can stop the process immediately if needed.
Laser Safety Enclosure: The laser beam is enclosed to protect workers from accidental exposure.
Fume Extraction: A system is used to remove any harmful fumes produced during the repair.
6. Fixtures and Clamps:
Secure Positioning: Fixtures and clamps hold the mould firmly in place during the repair.
Precision: These tools ensure the mould is perfectly positioned so that the robotic arm and laser can do their work accurately.
By bringing all these parts together, automating laser technology for mould repair provides a fast and accurate solution for fixing moulds.
Benefits of Automating Laser Technology for Mould Repair
Automating laser technology for mould repair offers several key advantages for manufacturers, especially those that rely on high-quality plastic parts:
Increased Efficiency: Automation speeds up mould repair by using robotic arms and vision systems, cutting down manual tasks and boosting production times—ideal for industries like automotive and electronics.
Improved Accuracy: Robotic systems perform repairs with higher precision than humans, restoring moulds to exact specifications and preventing defects, which is crucial for any plastic injection mould manufacturer in India.
Consistency: Automation ensures consistent quality in repairs, eliminating human errors and reducing the chances of defects or rework.
Reduced Labor Costs: Automating repetitive tasks lowers the need for skilled labor, resulting in cost savings, especially in plastic manufacturing companies in India.
Improved Safety: Automation reduces the need for human involvement in hazardous tasks, enhancing workplace safety.
Steps to Automate the mould Repair Process with Laser Welding
Automating the mould repair process using laser welding involves a few important steps.
Here’s a simplified version:
Process Analysis and Planning:
Identify Tasks: Look at your current mould repair process and decide which parts can be automated, like handling materials, positioning, welding, or inspection.
Define Goals: Set clear goals for automation, such as making the process faster, more accurate, and consistent.
Choose the Right Equipment:
Laser Welding System: Pick a laser welding system that suits the materials of your moulds and repair needs, considering power, beam quality, and automation features.
Robotic Arm: Select a robotic arm that can handle the weight of the mould and the laser welding head, while being precise.
Vision System: Choose a vision system that can detect and locate damage on the mould accurately.
System Integration:
Mechanical Setup: Connect the robotic arm, laser welding head, and vision system to work together.
Software Integration: Use or create software that controls the robotic arm, sets laser settings, and processes data from the vision system.
Programming and Calibration:
Teach Points: Program the robotic arm to move to specific areas of the mould, such as damaged spots for repair.
Laser Settings: Set the right laser power, pulse, and focus for the material being repaired.
Calibration: Adjust the vision system to correctly spot damage and guide the laser beam to the right place.
Testing and Simulation:
Simulate: Run a simulation of the automated repair process in software to check for any problems.
Test: Try the automated system on real moulds to see if everything works accurately and efficiently.
Training Operators:
Training: Create a training program for operators to teach them how to use the automated system.
Safety: Ensure that operators understand safety rules and know what to do in case of an emergency.
Continuous Improvement:
Analyze Data: Keep track of the system’s performance to spot areas where it can be improved.
Maintenance: Set up regular maintenance for the equipment to keep it running smoothly.
Stay Updated: Keep up with new advances in laser welding and automation to upgrade the system when needed.
Following these steps will help manufacturers successfully automate mould repair with laser welding, improving efficiency, and quality, and reducing costs.
Applications of Automated Laser Welding for Mould Repair
Automated laser welding technology offers numerous applications in the plastic industry.
Here are some key areas where this technology can be applied:
1. Repairing Cracks and Holes
Cavity Cracks: Cracks in mould cavities can be repaired quickly and efficiently using laser welding, ensuring the production of defect-free plastic parts.
Gate and Runner Holes: Damaged or worn gate and runner holes can be restored to ensure the proper flow of molten plastic material.
2. Restoring Worn Surfaces
Cavity Walls: Worn or eroded cavity walls can be resurfaced using laser welding, maintaining the desired surface finish and dimensional accuracy of the plastic parts.
Gate and Runner Channels: These critical parts of the mould can be restored to improve the flow of plastic material and prevent defects.
3. Modifying mould Geometries
Adding or Removing Features: Laser welding can be used to modify moulds by adding or removing features, allowing for the production of new or modified plastic parts without creating new moulds.
Adjusting Dimensions: Minor adjustments can be made to the mould dimensions to accommodate changes in product design.
4. Repairing Inserts and Cores
Metal Inserts: Damaged or worn metal inserts can be repaired using laser welding.
Plastic Cores: Laser welding can also repair cracks or defects in plastic cores, ensuring the integrity of the mould.
5. Routine Maintenance
Regular maintenance using laser welding can help prevent wear and tear, extending the lifespan of moulds and reducing downtime.
This is particularly valuable for plastic injection mould manufacturers in India, where minimizing production delays is critical.
Expert in Mould Repair with Automated laser Technology
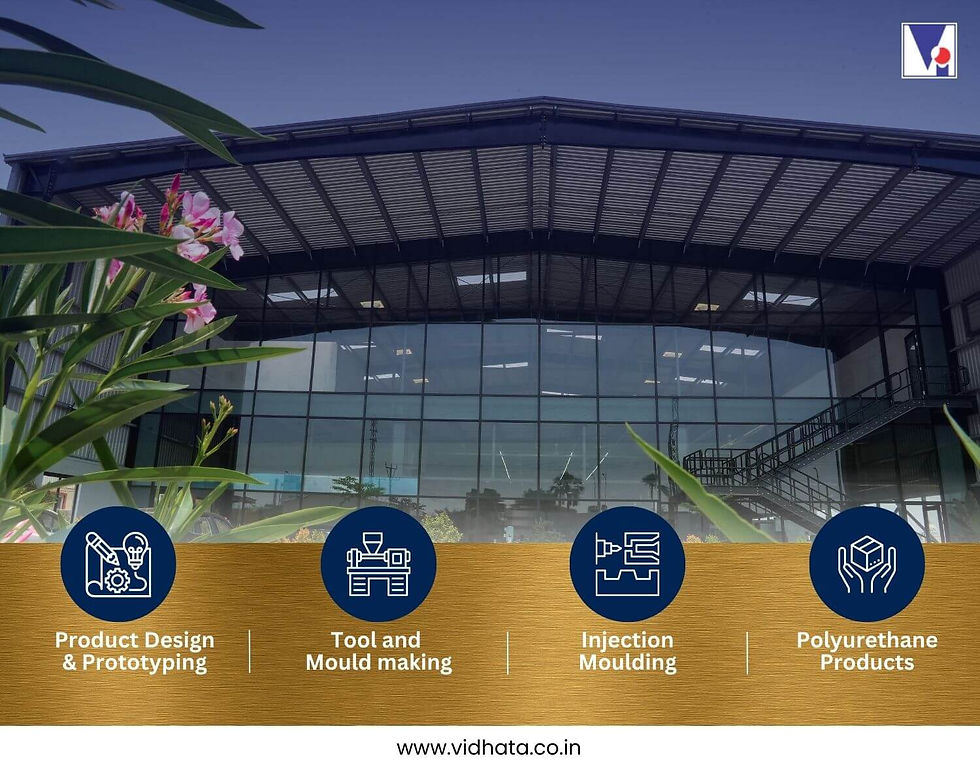
When it comes to advanced mould repair technologies, Vidhata Plastics stands out as a leader in India’s plastic manufacturing industry. As a top plastic injection mould manufacturer in India, Vidhata Plastics is at the forefront of using automating laser technology for mould repair. With cutting-edge robotic systems and state-of-the-art laser welding technology, Vidhata Plastics ensures that its clients benefit from the highest quality repairs, reduced downtime, and increased production efficiency.
Whether you are in the automotive, electronics, or consumer goods sector, Vidhata Plastics offers customized solutions for mould repairs, ensuring your moulds are always in optimal condition.
Conclusion: The future of mould repair lies in automating laser technology for mould repair. This innovative approach offers manufacturers increased efficiency, improved accuracy, and significant cost savings. For businesses in industries like automotive, electronics, and consumer goods that rely on high-quality plastic parts, investing in automated laser technology is a strategic move.
If you are looking for a reliable plastic injection mould manufacturer in India, Vidhata Plastics provides industry-leading mould repair solutions using the latest laser welding technology. Ensure the longevity and precision of your moulds by partnering with a company that understands the importance of cutting-edge repair technology. Contact Vidhata Plastics today to learn more about how we can support your plastic manufacturing needs.
Visit Our Website: https://www.vidhata.co.in/
Contact Us: https://www.vidhata.co.in/contact
Email Id: info@vidhata.co.in
WhatsApp No. : +919550665666
Kommentare